oUR sERVICES
What do we Offer?
Fermi Solutions provides an array of specialized services to the nuclear sector, that emphasize regulatory and design standards compliance. Our work is focused on providing Engineering Design Services and Field Engineering Services for on-site expertise and project facilitation.  In addition, we also provide equipment condition assessments for operational and fitness for service reliability, innovative Reactor Tooling solutions, Inspections reviews and Fitness for service, Generator and Excitation Systems, and Technical Training. These services are delivered with a commitment to safety, innovation, and superior performance standards.
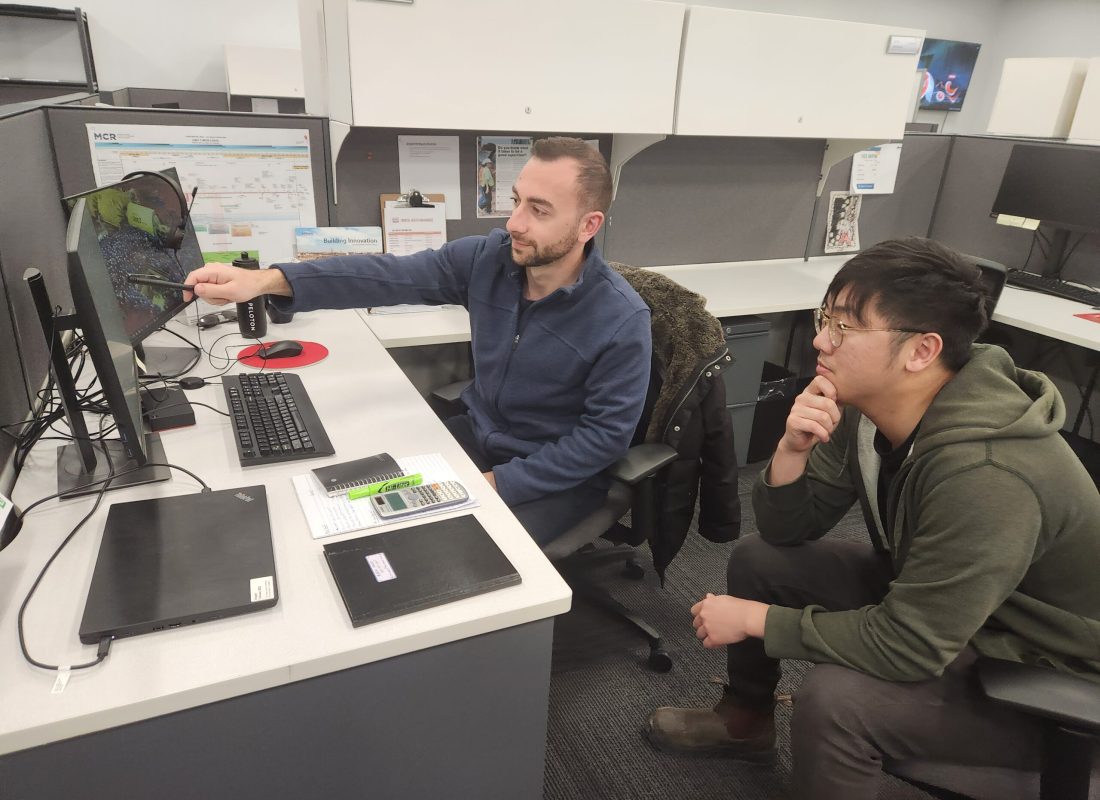
Design Services
We provide compliant Engineering Change Control services aligned with clients' process, including engineering change paper and CNSC Licensing interface support. Our services include Design Engineers, Owner’s Engineering Leads, backed by our technical expertise. As part of the services, we complete Design Calculations, Engineering Evaluations, Technical Reports, Engineering specifications, pressure boundary and code compliant designs including N285.0, ASME SEC III, B31.1 codes.
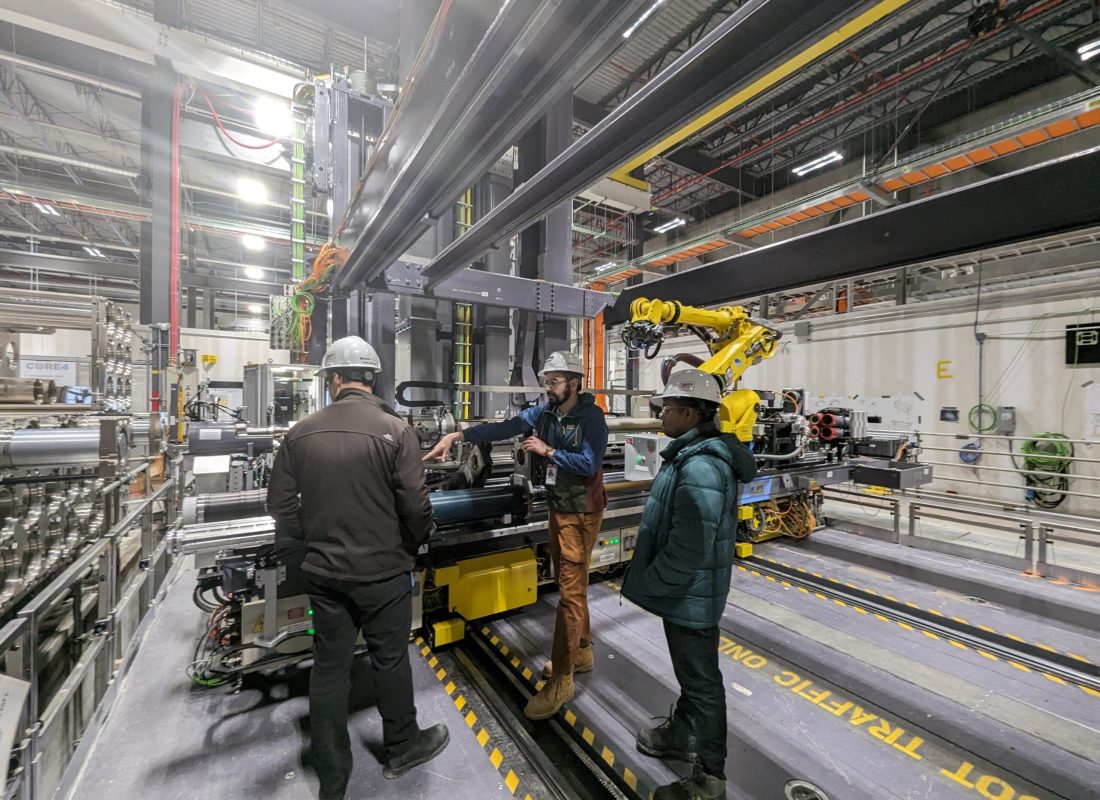
Field Services
We boast extensive experience in successful nuclear industry field deployments. Our services encompass Project and Field Engineers, deployment of Technical Experts, and comprehensive planning for system installation, commissioning, and turnover.
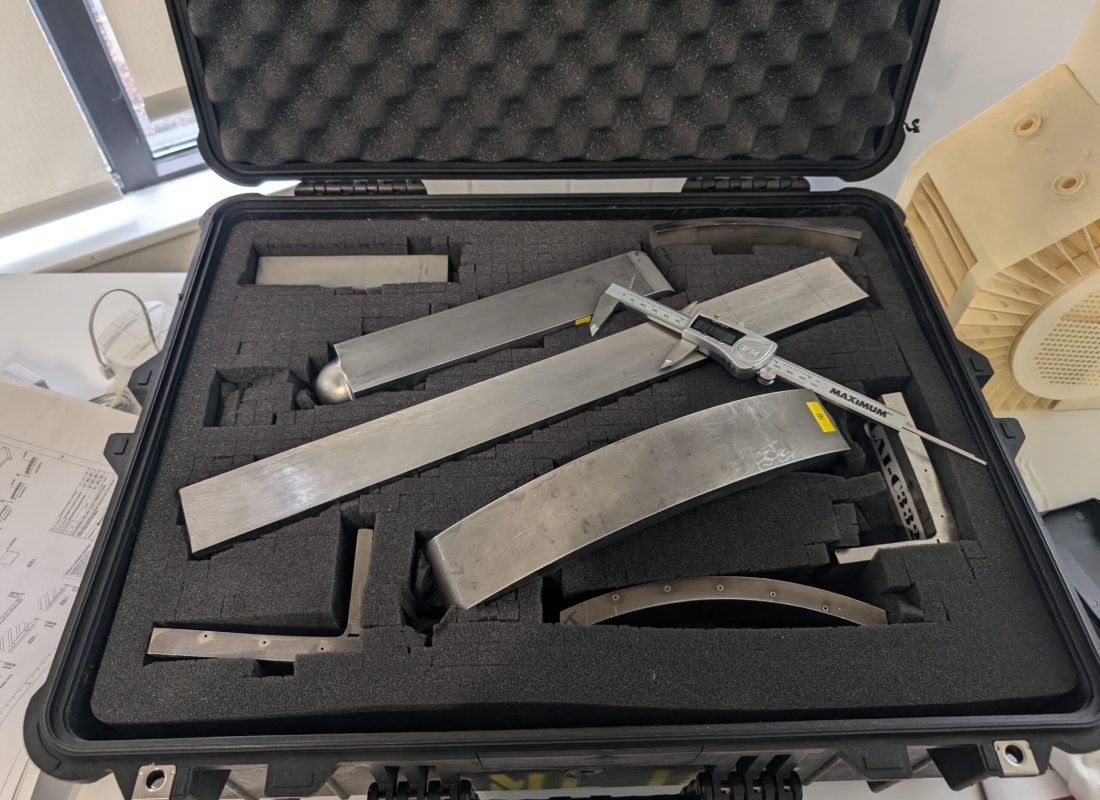
Equipment Assessment
We offer equipment condition assessment support, leveraging technical experts for troubleshooting and resolution. Services include on-site troubleshooting, root cause investigations, high-impact team investigations, adverse condition monitoring plans and equipment deficiency reduction.
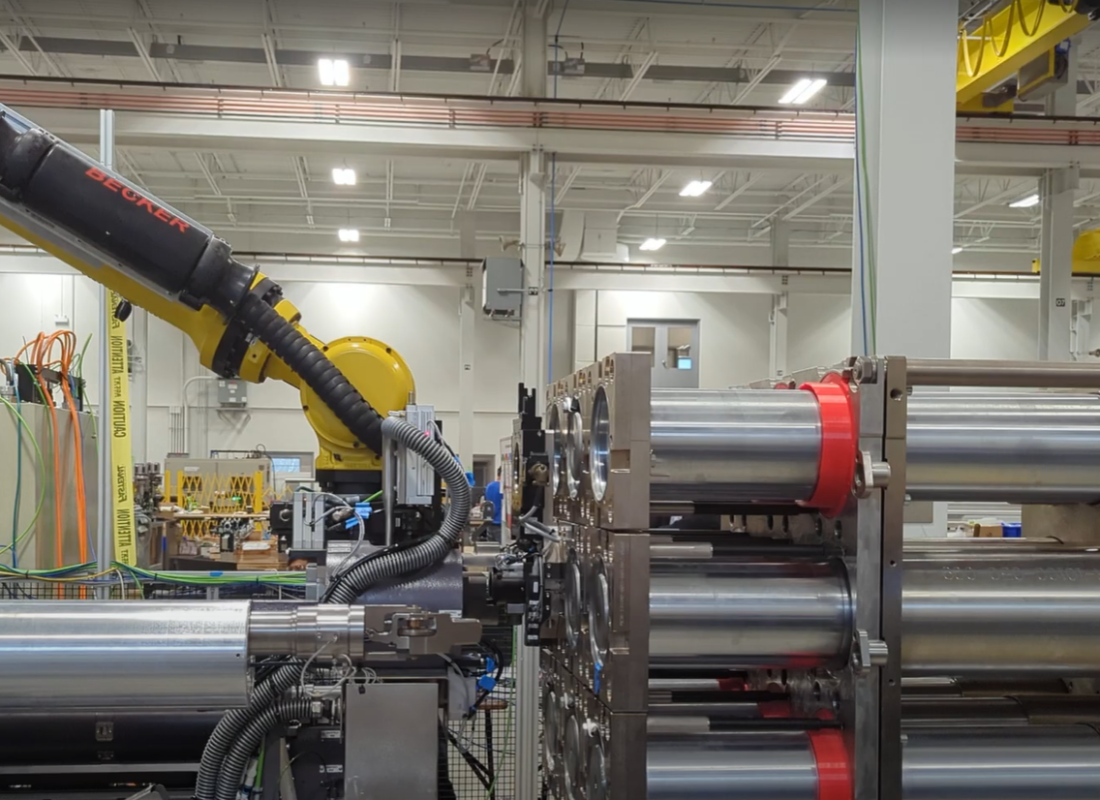
Reactor Tooling
We support development of innovative maintenance and custom reactor tooling. Our product development team collaborates with manufacturers and designers to deliver tailored tooling solutions, including system integration engineering, writing up of the test plans and supporting Factory Acceptance Testing and field deployment.
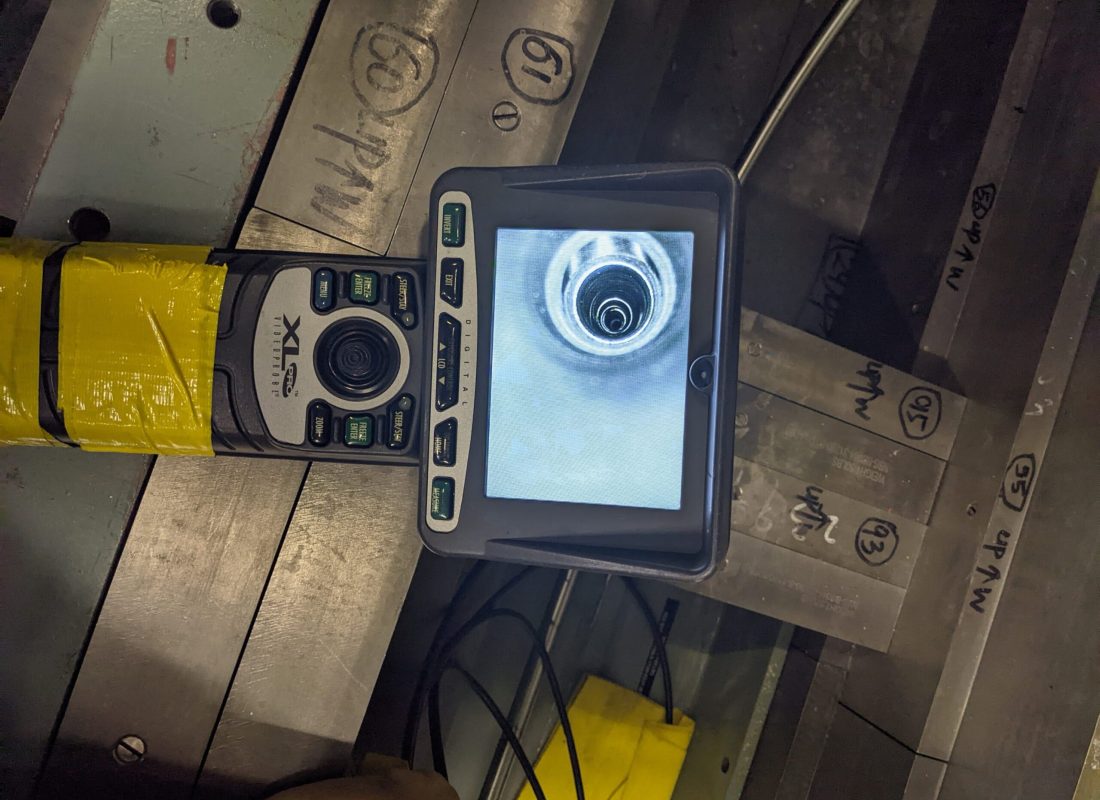
Inspections and Fitness for Service
We deliver specialized ‘Inspections and Fitness for Service’ solutions, providing detailed assessments and evaluations to ensure the integrity and reliability of plant components following ASME SEC XI standard. We optimize safety and performance, adhering to industry standards to extend the life of reactor components and piping systems.
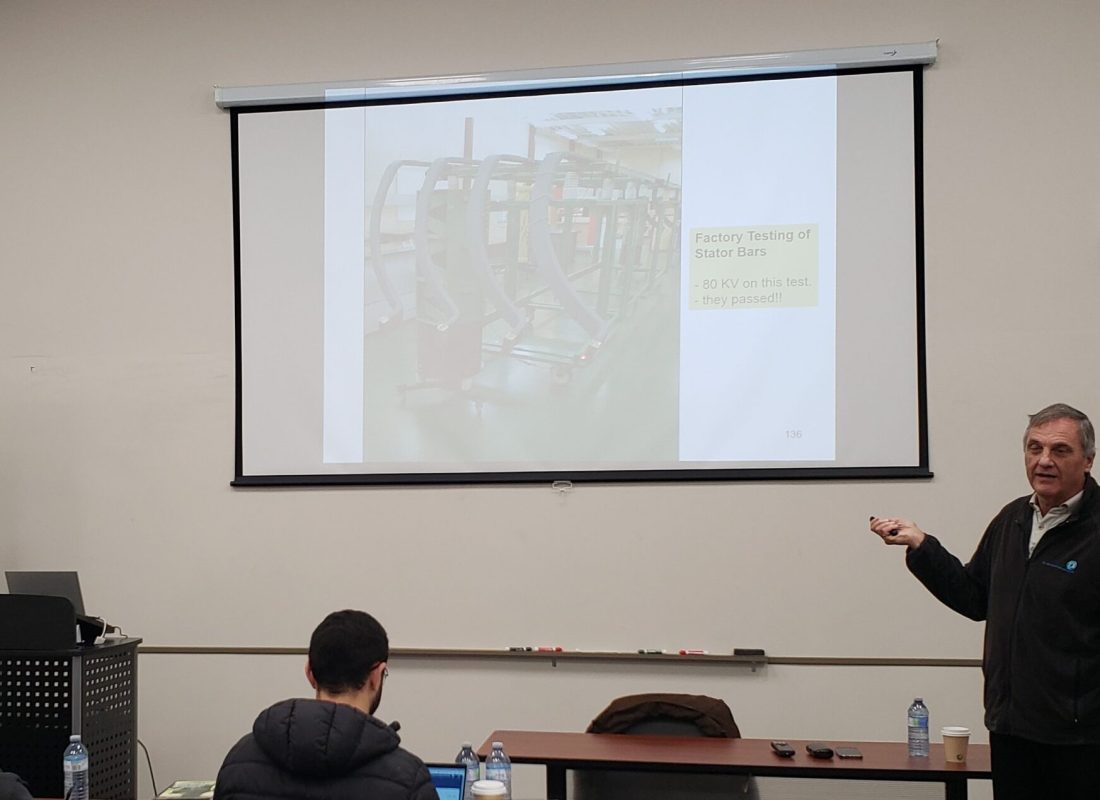
Technical Training
We provide targeted industry-specific training to boost your team's expertise and efficiency, promoting operational excellence through professional development. We also provide courses and technical training on Generators and Pressure Boundary Systems.
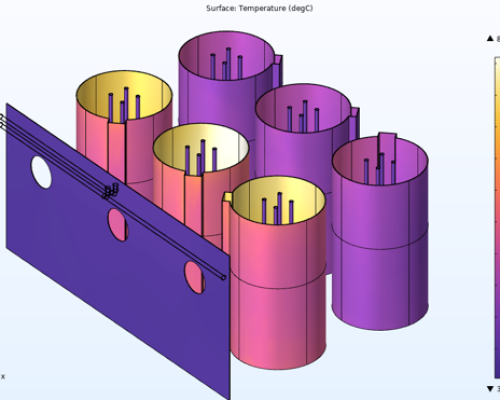
Engineering Analysis
We utilize COMSOL Multiphysics Finite Element Analysis software to perform electromagnetic analysis and a variety of other assessments for clients in the nuclear industry. This software enables us to thoroughly examine the electromagnetic characteristics of any critical system, including magnetic flux strength, resistive heating, temperatures, and eddy current losses. Additionally, our capabilities extend to Electro Magnetic Modelling, Stress Analysis, Engineering Calculations, and Radiation Modelling, providing a comprehensive understanding of each project's unique demands.
Our Projects
Our Recent Project Successes
REACTOR TOOLING
- Bruce Power MCR Dose Reduction Laser Ablation Tooling
- Bruce Power MCR Automatic Feeder Removals Tooling
- Bruce Power U7 Calandria Relief Duct (CRD) Inspections and Repair Tooling
- Vertical Flux Detector & Weld Tube Bundle Extraction Tooling
NUCLEAR
- Bruce Power Lu-177 Isotope Production System
- Bruce Power U3 PHT Chemical Decontamination for Dose Reduction
- Bruce Power U5 Power Recovery Program
CONVENTIONAL
- Generator - Stator & Rotor Rewind
- Power (MW) Recovery Program
- Root Cause Investigations
- DCC Boiler Level Controller Software Fix (ECC Support)
SPECIALTY
- NFM Removal Concept Design
- Engineering Change Control Process Consultation
- N299.1 Procedural Consultation
- CNL Whiteshell Laboratories Decommissioning - Procedure Consultation
LEARN MORE ABOUT OUR PROJECTS
The U3 Chemical Decontamination project, spearheaded by Fermi Solutions project team, achieved remarkable success. By significantly reducing radiation exposure for personnel involved in U3’s Major Component Replacement (MCR3) program at Bruce Power, this project enabled the seamless commencement and continuation of critical operations for the client. The deployed system effectively chemically removed accumulated radioactive crud from the Primary Heat Transport (PHT) system. The captured crud was safely disposed of, resulting in substantial dose reduction for personnel.
Highlights:
- Concept to Execution: We collaborated closely with the vendor to help to bring the CAMDA chemical decontamination system to life. The system was meticulously manufactured and deployed into Bruce Power’s BB station in Unit 3.
- Stakeholder Alignment: Fermi Solutions provided comprehensive services, including Owner’s Engineering Support, Field Engineering Support, and Project Integration. Our goal was to ensure seamless collaboration among all stakeholders, including Bruce Power and vendor partners.
- Troubleshooting and Resolution: Throughout the project, Fermi Solutions offered ad hoc troubleshooting and swift issue resolution during field support.
From concept development to execution, commissioning, and successful turnover, Fermi Solutions played a pivotal role in driving the project’s success. Unilateral agreement on the project’s success across the board has meant this system will be deployed at Unit 4 in preparation of MCR4 as well as be a preferred method of decontamination for other Bruce Power units.
During 2020-2021, Fermi Solutions spearheaded a groundbreaking initiative to address reactivity mechanisms removal within Bruce Power’s Unit 6 reactors as a pre-requisite for the deployment of Permanent Start Up Instrument (PSUI) system. Our comprehensive approach encompassed conceptualization, design, manufacturing, and successful deployment of the custom-built Volume Reduction System (VRS).
Building on our success, Fermi Solutions replicated the effort in Unit 7 in 2021-2022 timeframe. The removal of Well Tube Bundles (WTBs) that Reactivity Mechanisms such as vertical flux detectors (VFDs), helped  prepare the VFD location for the deployment of the Lutetium-177 (Lu-177) Medical Isotope Production System (IPS). This critical system enables Bruce Power to produce life-saving medical isotopes, benefiting people worldwide.
Highlights:
- Reactivity Mechanism Reduction: The VRS was meticulously designed to volume-reduce reactivity mechanisms critical to reactor operation. By repurposing Vertical Flux Detector (VFD) locations, we successfully removed well tube bundles (WTBs) – the very RMs residing within these locations. These WTBs were then safely deposited in an underground repository, significantly enhancing safety and efficiency.
- Ongoing Innovation: The VRS, now widely accepted as an excellent tool, continues to evolve. It adapts to accommodate volume reduction of several other Reactivity Mechanisms, including Horizontal Flux Detector assemblies. As global demand for medical isotopes rises, Fermi Solutions remains committed to providing future solutions for the removal of all other Reactivity Mechanisms.
- Concept to Execution: Fermi Solutions played a pivotal role from the Concept Phase, leading the development of removal methods and disposal strategies. Our expertise as the Subject Matter Expert in tooling solutions for reactivity mechanism removal at large nuclear reactors ensures continued success.
The Lu-177 IPS project marked a significant milestone in medical isotope production. Our comprehensive approach encompassed designing, manufacturing, and deploying critical components for the Isotope Production System (IPS).
Let’s delve into the project highlights:
- Concept to Deployment: The IPS was meticulously conceptualized and designed by IsoGen, a joint venture formed by Kinectrics and Framatome. Our role as Project Integrator was pivotal in ensuring successful project delivery.
- Bruce Power’s Unit 7 Deployment: The IPS found its home at Bruce Power’s Unit 7. Our relentless efforts spanned field engineering leadership, design engineering, and owner’s engineering support. As a First of A Kind (FOAK) project, it required innovative troubleshooting and swift issue resolution.
- Isotope Production: The IPS, now fully functional, produces the radionuclide Lu-177 via neutron capture within the reactor core. This life-saving medical isotope is harvested and shipped off-site weekly. It plays a crucial role in treating advanced cancers worldwide.
- Project Integration: Fermi Solutions leads ongoing efforts in project integration between the vendor IsoGen and the client Bruce Power. Our goal is to ensure the project is delivered within budget, issue-free, and on time for the ongoing Lu177 IPS system expansion in Unit 7. This expansion is forecasted to double the capacity of the existing system by the last quarter of 2024.
Our commitment to excellence and safety remains unwavering as we continue to contribute to groundbreaking advancements in medical science.
The Calandria Relief Duct Inspection Project was a critical endeavor aimed at ensuring the integrity and safety of the Calandria Relief Ducts Y1, Y2, Y3, and Y4.
Let’s explore the key aspects of this project:
- Visual and Volumetric Inspection: The project included the inspection of the calandria relief ducts, employing both visual and volumetric assessment techniques. This examination allowed us to identify any potential issues or anomalies.
- Reactor Tool Deployment: The project involved the design and deployment of the Moderator Inspection Eddie Current Tool. This specialized tool played a crucial role in assessing the condition of the relief ducts, providing valuable data for decision-making.
- Fermi Solutions’ Contributions:
- Design Engineering Support: Our experts provided design guidance, ensuring the inspection tool’s effectiveness and compatibility with the relief ducts.
- Project Integration Support: Fermi Solutions facilitated seamless collaboration among stakeholders, including the vendor and the client.
- Field Deployment Support: Our field engineers were on-site, overseeing the successful implementation of the inspection process.
- Vendor Assistance: Fermi Solutions assisted the vendor by acquiring essential information and developing scopes of work.
The successful execution of this project contributes to the continued safe operation of the facility. Fermi Solutions remains committed to excellence in nuclear engineering and project management.
Our Recent Achievements
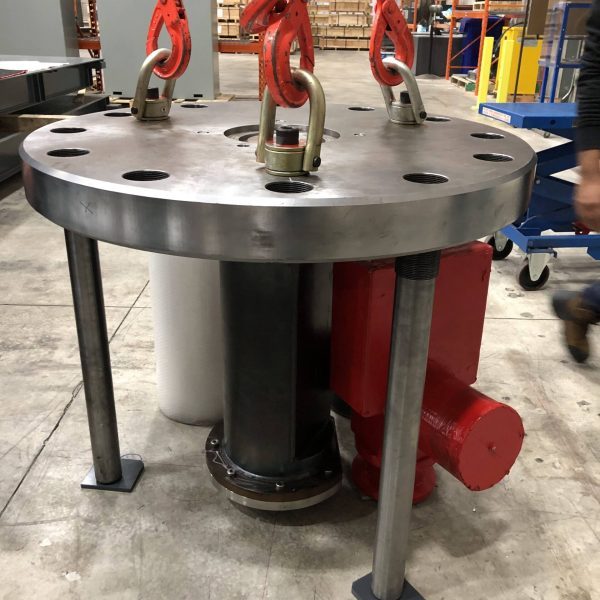
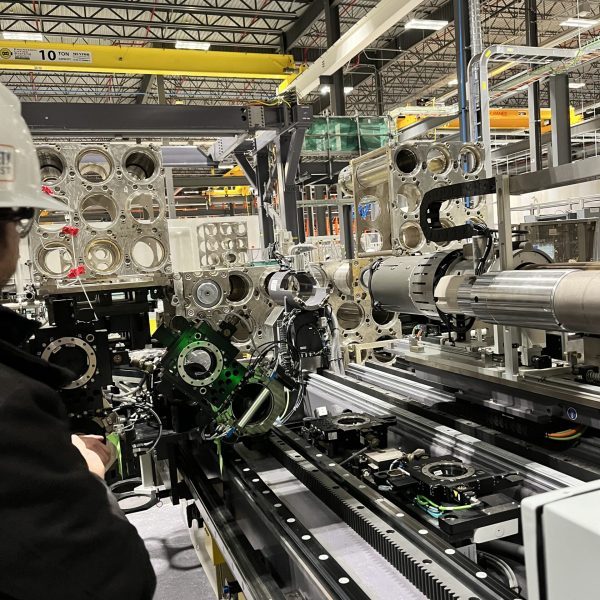
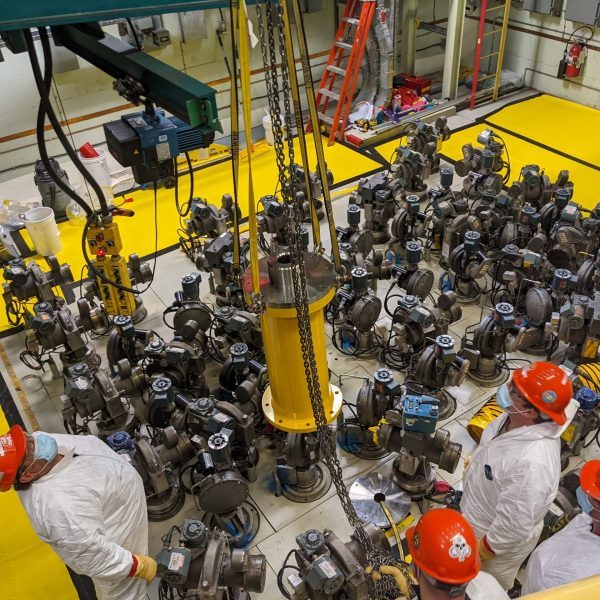
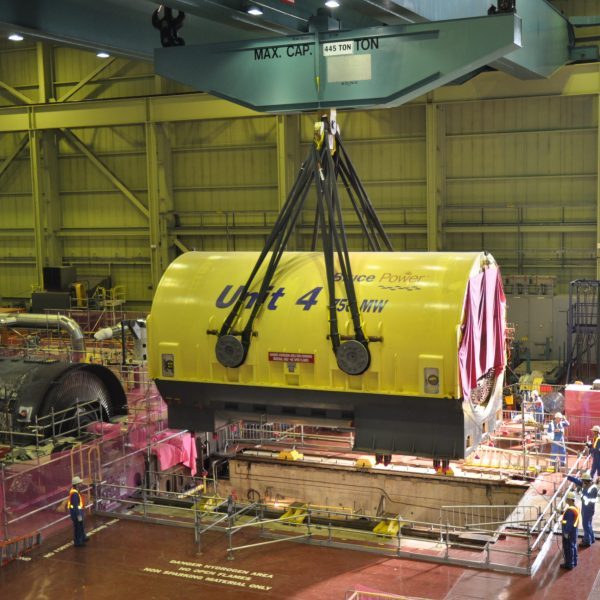
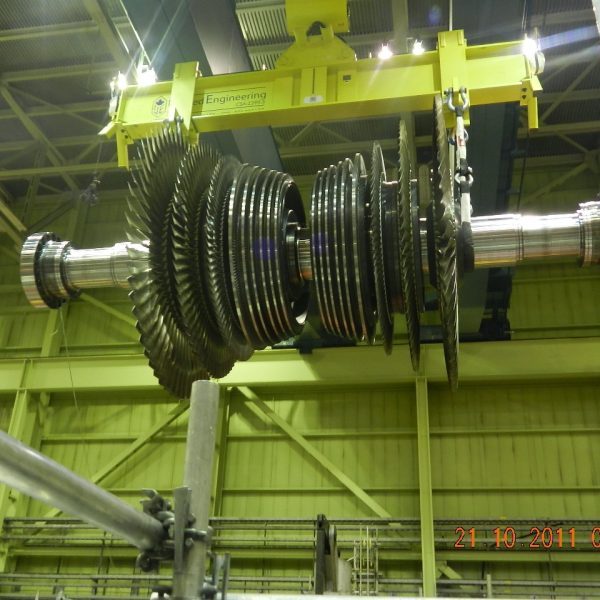
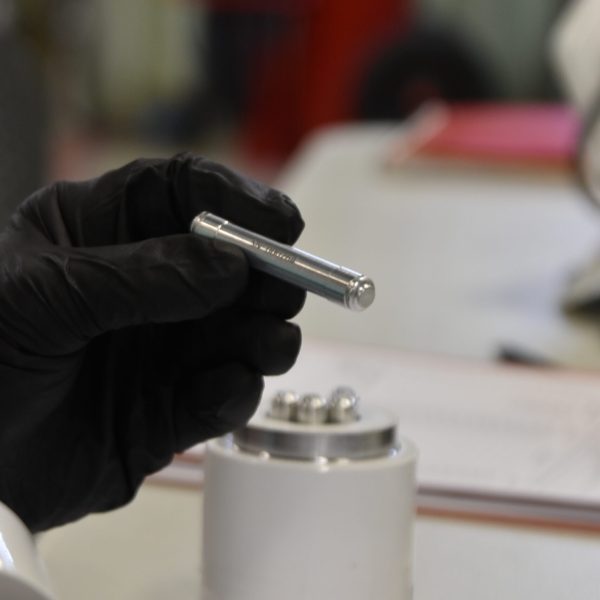
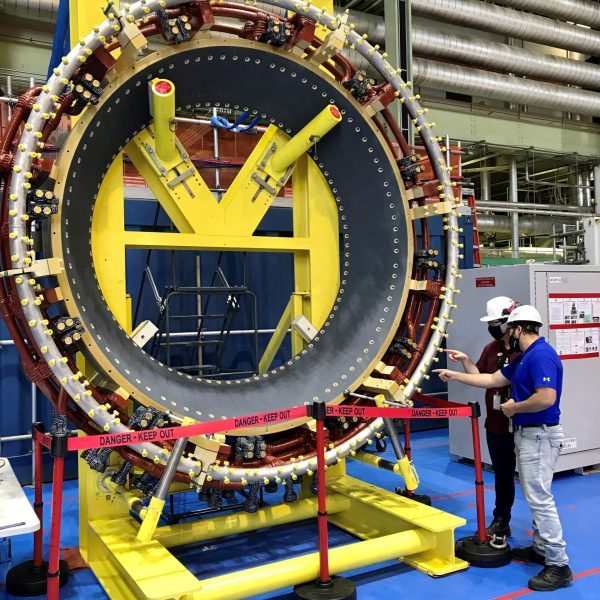
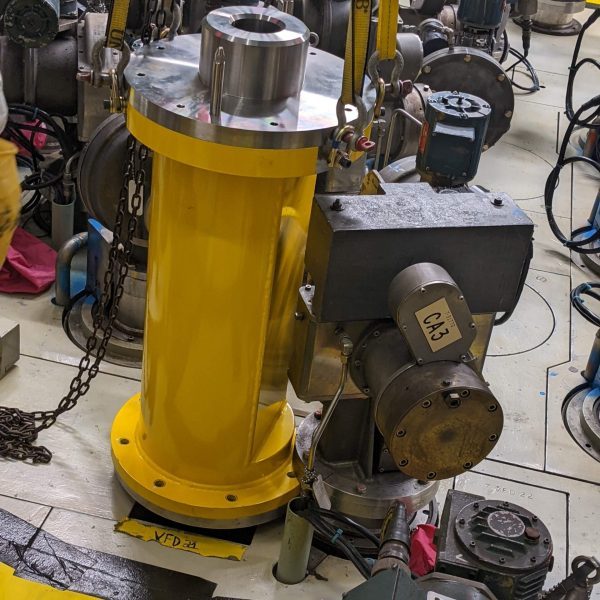